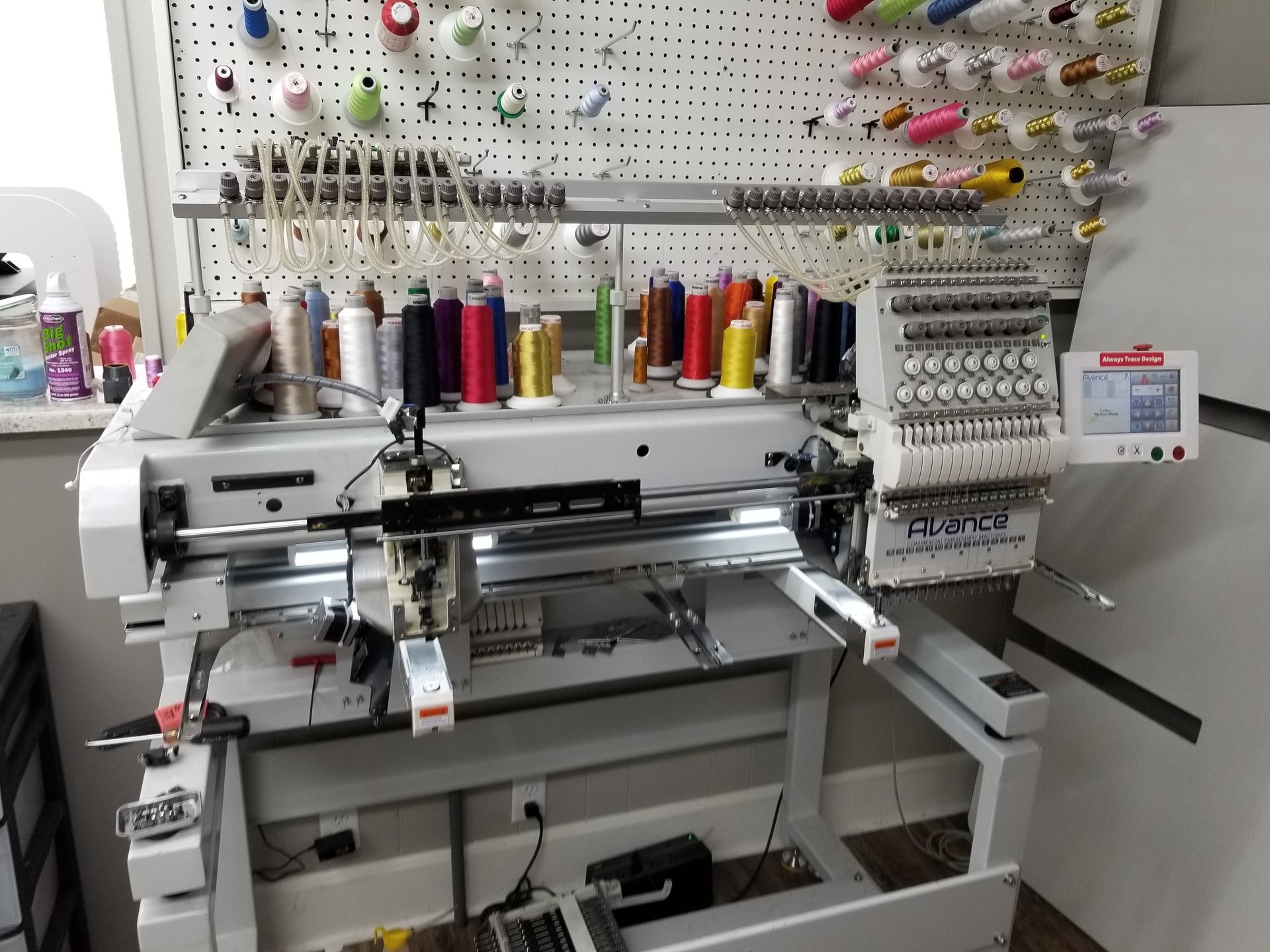
AJ's Stitching Time
Services, Repair, and Warranty Work
On-site Commercial Embroidery Machine Service, Warranty Work, and Repair, on most brands of machines.
Avance', Barudan, BAI, Butterfly, Dublin, Feiya, Happy, Highland, Mesa, Meistergram, Pantograms, Pro Capsule, Ricoma, SWF, Tajima, Toyota, and ZSK.
Embroidery Machine Service, and Repair
Expert repair and training for commercial embroidery machines available.
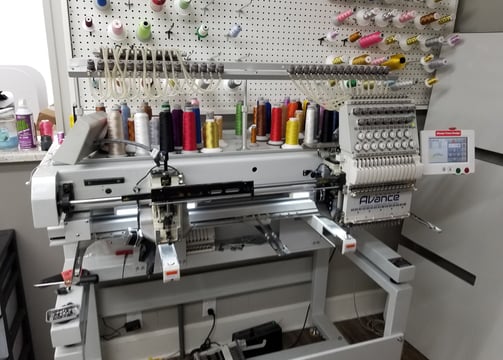
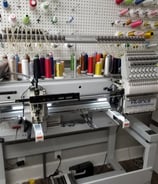
Machine Repair, Service, and Warranty Work.
On-site service for various embroidery machine brands offered.
Avance', Barudan, BAI, Butterfly, Consew, Dublin, Feiya, Happy, Highland, Melco, Mesa, Meistergram, Pantograms, Pro Capsule, Prodigi, Ricoma, SWF, Tajima, Toyota, Yamata, and ZSK.
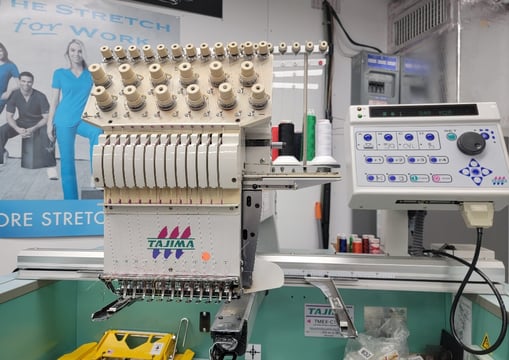
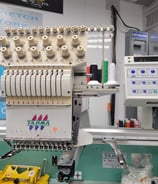
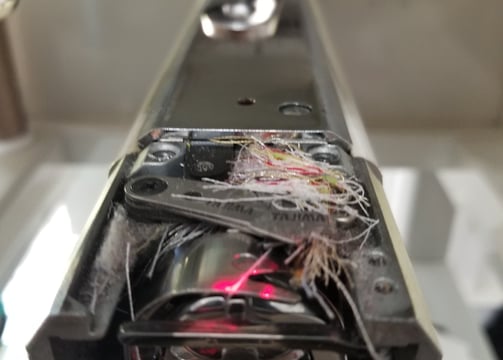
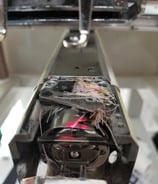
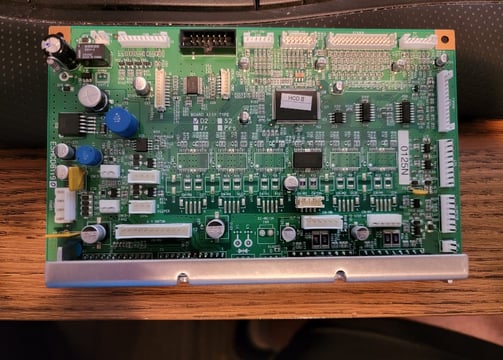
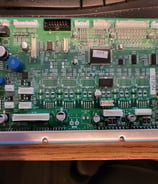
Brands of machines serviced.
Here is a list of embroidery machine brands that I work on.
Germany: ZSK,
Japan: Barudan, Happy, Tajima, Toyota,
Korea: SWF
Chinese: Avance', BAI, Butterfly, Dublin, Highland, Mesa, Meistergram, Pantogram, Pro Capsule, Ricoma, and any Chinese made embroidery machine that uses Dahao software.
Embroidery Machine Certifications and Approvals
I am currently certified, trained and/or approved as a technician for the following commercial embroidery machines. I am authorized to service, train and do warranty work on these machines.
2008: Toyota – Trained, and certified service and repair technician, rank A
2008: Happy – Certified and approved on single and multi-head machines.
2009: Meistergram - Trained, certified and approved on single and multi-head machines.
2009: Ricoma – Trained, certified and approved.
2013: ZSK – Trained, certified and approved on single and multi-head machines.
2014: Tajima – Approved by Hirsch.
2014: SWF – Approved by Stitch it International, Sew-tech, Coldesi and SWF Central.
Our Locations
We provide on-site embroidery machine service, repair and training services in the Continental United States of America for most commercial embroidery machine brands.
Service: On-site service available nationwide.
Hours: Mon-Fri 9am - 5pm
Here are some of the locations and areas that I have done training and service.
USS Dwight D. Eisenhower (CVN-69) an aircraft carrier currently in service with the United States Navy
USS Harry S. Truman (CVN-75) the eighth Nimitz-class aircraft carrier of the United States Navy
Black Daggers Parachute Demonstration Team Simmons Army Airfield, Fort Bragg, North Carolina
Marine Corps Air Station Beaufort
Parris Island, USMC Marine Base
HRT counter terrorist tactical team compound, FBI Academy in Quantico, Virginia,
Oklahoma State Penitentiary: Oklahoma Correctional Industries, Department of Corrections
Kansas Department of Corrections, El Dorado Correctional Facility (EDCF)
BUREAU OF CORRECTIONS, St. Croix, US Virgin Islands
MasterCraft Boats
Searay Boats
Chapparal Boats
Services
Expert embroidery machine repair and training services.
Contact
Support: Call Tracee at 678.431.1467
678.431.1467
© 2024. All rights reserved.